Case Study: Effective Tank Patch Repair for Tanks in Oil & Gas and Chemical Industries
Small cracks and pinholes within the tank can successfully be repaired using a composite patch repair. A repair patch made of carbon fiber and an immersion grade epoxy is not just a temporary repair; due to its high adhesion strength, outstanding tensile strength, and resistance to many aggressive chemicals, a composite repair patch can provide a service life extension up to 20 years for most applications.
Case Study: Repairing Small Diameter Tanks for Oil & Gas
Background
In this project, small diameter (10-foot) tanks which were procured from major oil companies, need repairs to be used by another operator. The aim was to repurpose these tanks to be fully operational and extend their life with a maintenance-free solution. After inspecting the tank, several issues were discovered, including through wall holes and major corrosion pitting.
Challenge
The tanks required refurbishment to be repurposed effectively. The leaks and deterioration from corrosion required an easy to apply and cost-effective solution that could address these issues efficiently.
Solution
The chosen solution was composite repair, which involved using reinforcing fabric and epoxy resin binder to restore the tanks’ structural integrity. Composite repair patches not only stopped ongoing corrosion but also acted as a barrier against further deterioration.
Installation
The installation process involved various steps to ensure thorough restoration. The tank floors were grit blasted and visually inspected for damage. Any identified through-wall failures were repaired using composites, structurally reinforcing the tank and stopping the leak.
After inspection and composite repairs, the tanks were flooded with epoxy to halt any ongoing corrosion, providing a protective barrier. This epoxy flood coat will effectively stopped further corrosion.
After grit blasting was complete, a single 10-foot diameter tank could be repaired in just 2 hours. Environmental control wasn’t cost-effective, so work was limited to early mornings and late evenings to deal with the sweltering Texas summer.
Advantages
Composite installation constitutes a cold process that leaves internal tank coatings unaffected. Their inherent flexibility ensures a seamless fit to tanks of diverse shapes and sizes, all while being compatible with corrosion prevention systems like coatings and cathodic protection. Carbon fiber based composites even outperform carbon steel in mechanical performance due to their significantly higher fatigue resistance and ultimate tensile strength. Moreover, it has excellent resistance to vibrations, thermal cycles, or other variable loadings, which is bolstered by its outstanding chemical resistance. Additionally, these repairs have a 20-year maintenance-free service life.
Case Study: Roof Repair for Fiberglass Chemical Storage Tanks
Background
This project included a chemical distribution facility that housed older fiberglass chemical storage tanks.
Challenge
These tanks were grappling with degradation caused by chemical and UV exposure, resulting in issues like cracking and delamination. The specific focus was on the roof and side walls of the tanks. The facility required a solution that provided long-term reinforcement and that could be installed while the tanks were online.
Solution
The identified solution was a long-term reinforcement strategy that would not only address the existing issues but also withstand chemical exposure. Crucially, the chosen solution had to accommodate the requirement for online installation, allowing the tanks to remain operational during the reinforcement process. The chosen carbon fiber composite system also had a high modulus, excellent adhesion, and long-term fatigue resistance.
Installation
The reinforcement was successfully installed without the need for scaffolding, which lowered the overall cost of the repair.
Installation Steps:
- 60-grit sandpaper was used to aggressively sand the fiberglass.
- FRP Repair Putty was applied to fill in any cracks and/or holes and smoothly transition any hard edges.
- FRP 120 HT Adhesive was applied via brush/roller at 5 – 10 mils.
- The CF-500 BD was saturated with FRP 211 HT Saturant and applied over the repair areas in multiple layers.
- HP 300 Epoxy was then used to topcoat the repair area and allowed to cure for 24 hours.
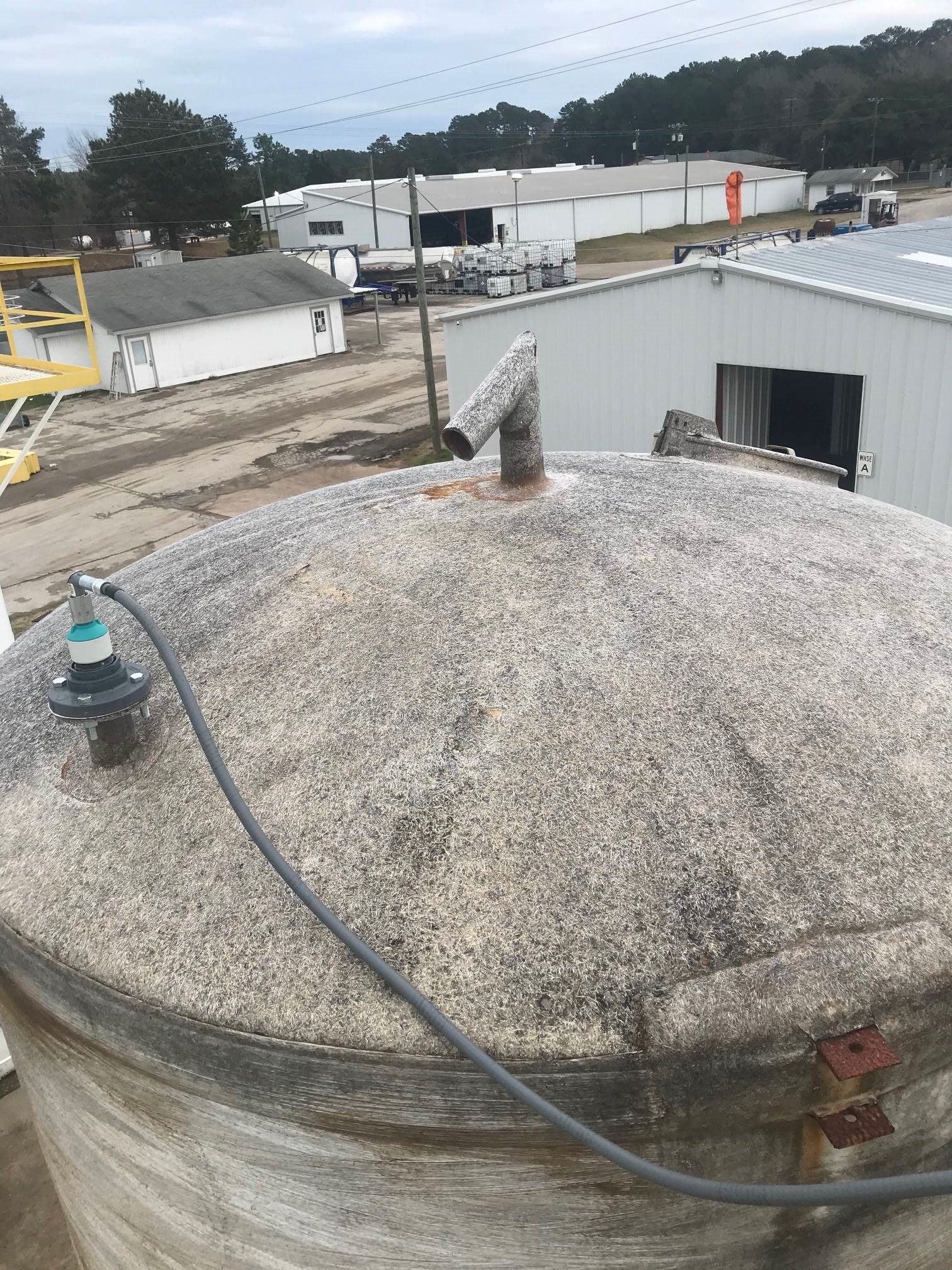
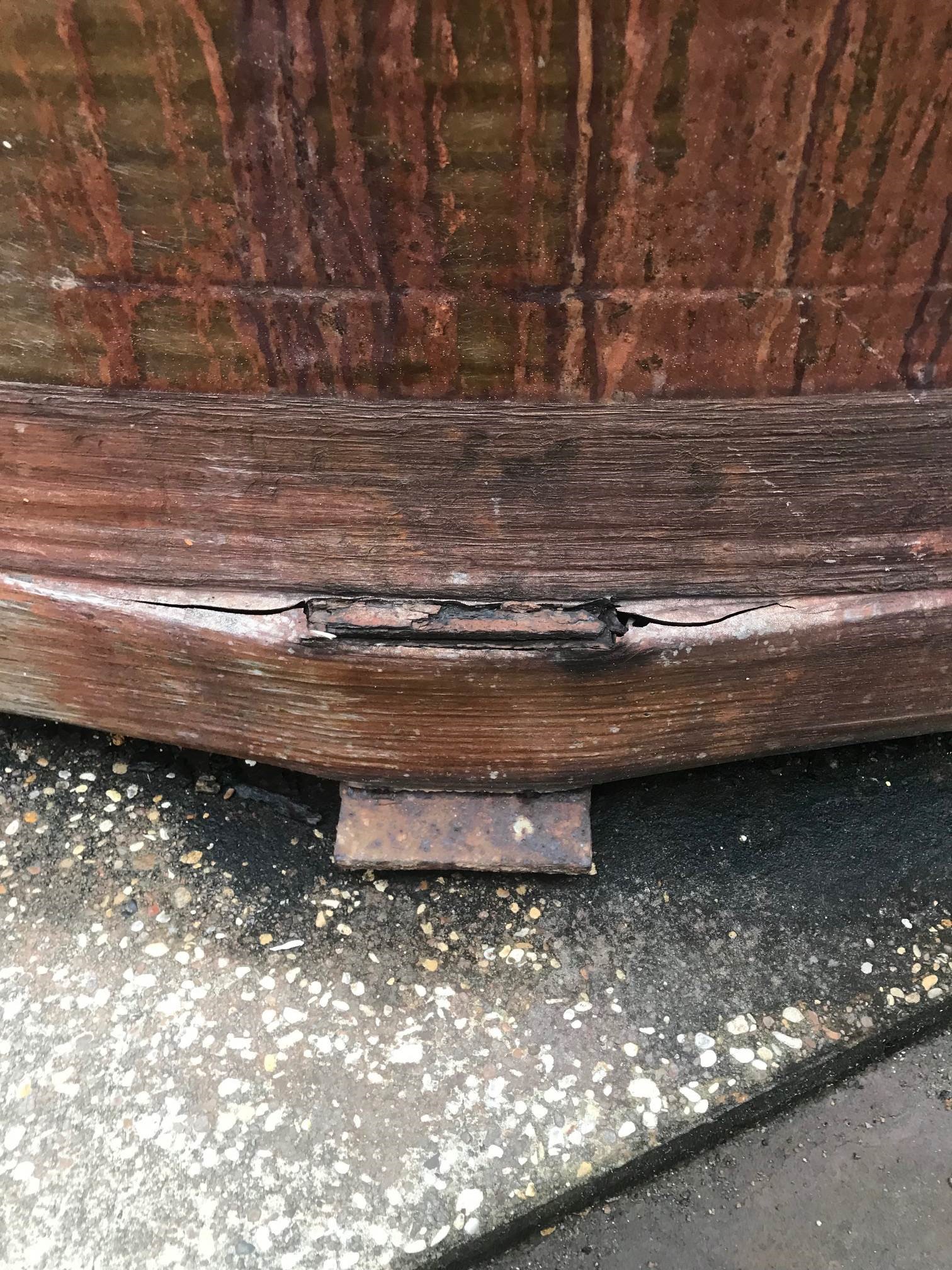
Advantages
The chemically resistant composite system not only extended the service life of structures by an estimated 20 years but also eliminated the need to drain tanks during the project. The epoxy-based resin system also allows for remarkable adaptability. By accommodating a wide range of application temperatures and humidity levels, the system eliminates the need for costly environmental controls. On top of that, the composite can be installed via wet lay-up, which ensures a perfect fit for all repair shapes and orientations.
Balancing cost-effectiveness with long-term performance, tank patch repair addresses the structural vulnerabilities of aging tanks and pipelines. With its proven advantages, this technique is more than a quick fix; it’s a steadfast investment in the future of industrial structures.
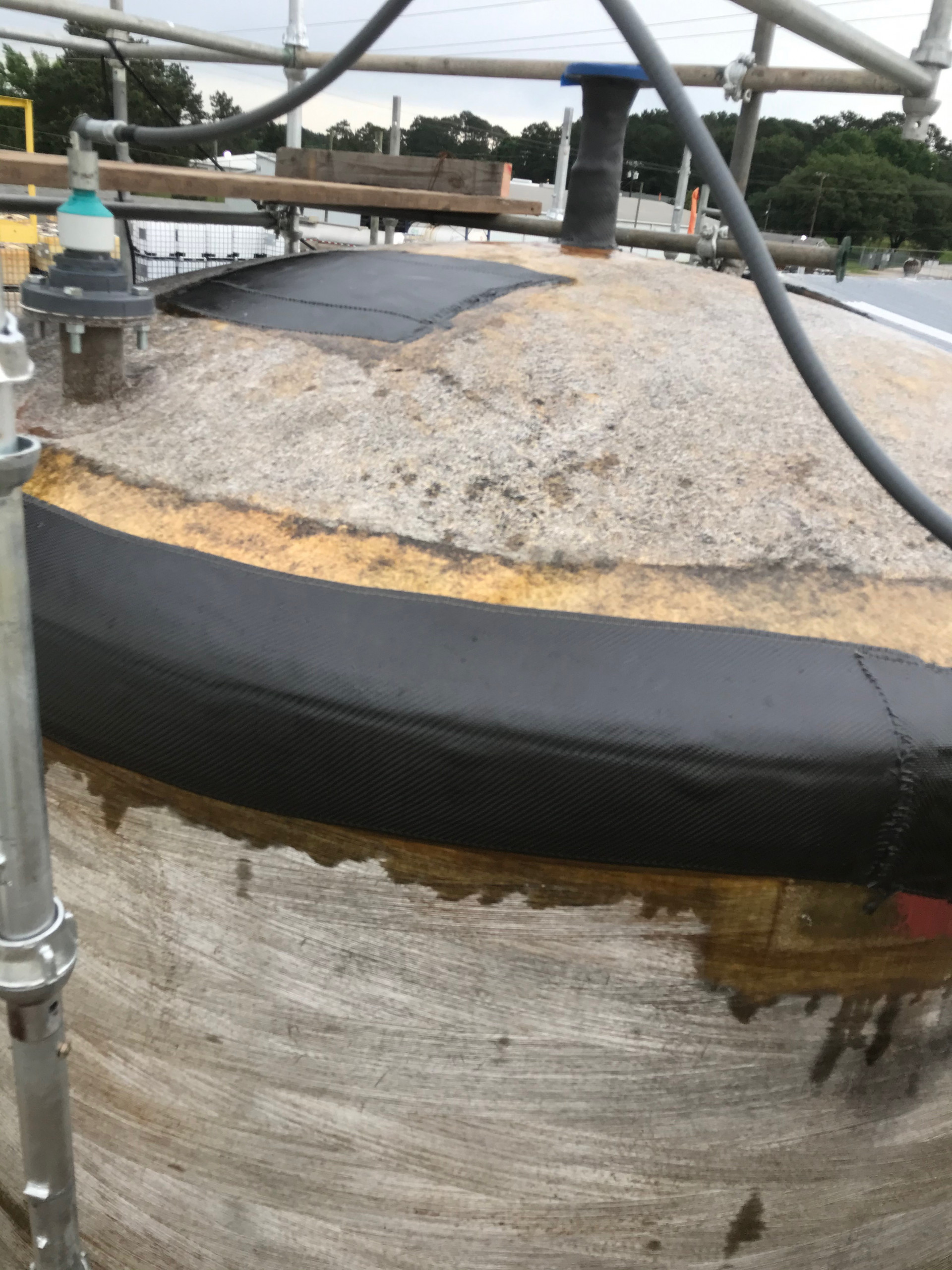
Case Study: Pulp and Paper Scavenger Tank Spot Repairs
Background
A pulp and paper facility had a large scavenger tank that was experiencing corrosion and buckling plus some pinhole leaks. A corrosion assessment showed that the tank only required spot reinforcement. The mill was looking for a solution that would both structurally reinforce the tank and address the corrosion and the pinhole leaks.
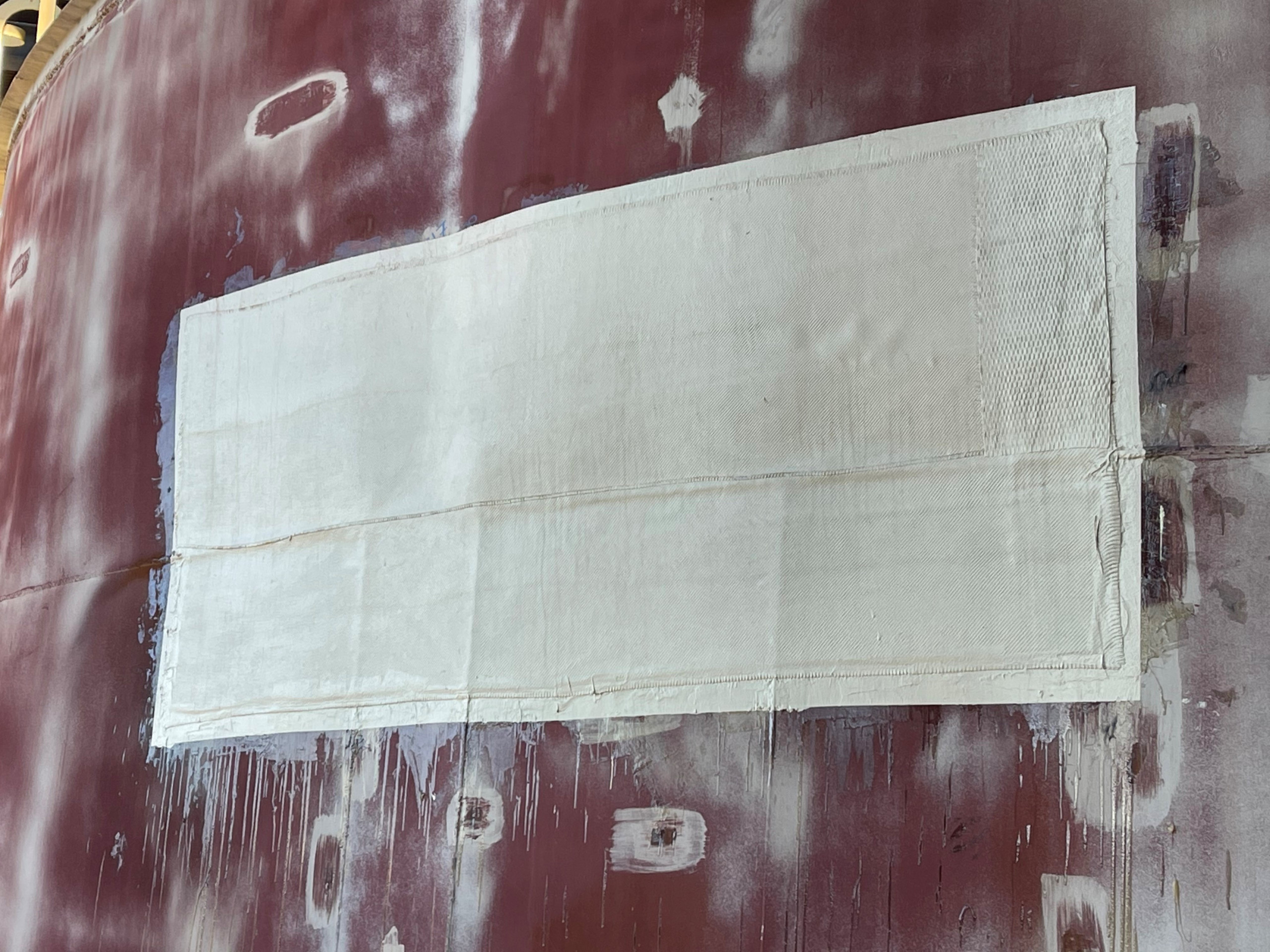
Solution
An 8 ft x 12 ft composite carbon fiber patch was an excellent option instead of externally welding steel plate. The repair used FRP Repair Putty, CF-500 BD fabric, FRP 210 HT, and HP-400 Novo. The bidirectional fabric used in the repair is highly versatile and easy to install, which was an appropriate fit for this project’s needs.
Advantages
Replacing the tank would have incurred significant costs, and other repair alternatives, such as welding steel plates, was not a good option for the mill because of the danger welding posed to harming the internal coating of the tank. Using composite repair with a cold application process and lightweight materials meant the internal coating was protected, and the application could be completed without the support of a crane. The composite repair was also applied with the tank was still in service, and it will provide a structurally-reinforcing, maintenance-free, 20-year extension to the tank’s service life.
To learn more about our tank patch repair services, contact us for a free consultation.
Having Issues with Pipe Corrosion or Erosion?
Contact us for a free evaluation!
X