Background
Operating and maintaining underground high-voltage transmission lines in a major urban area is a huge challenge for any utility provider, as reliability and availability are of the utmost importance. A New York City-based electricity, steam, and natural gas provider owning and operating approximately 680 circuit-miles of underground pipe-type cables often experienced multiple dielectric fluid leaks per month. Many of their high-pressure, fluid-filled (HPFF) transmission lines were over 50 years old and worn due to environmental factors such as stray current, leaking water and sewer lines, and highly-corrosive soil.
Due to external corrosion, many sections on the pipes developed through-wall failures. As the HPFF lines contain a hydrocarbon-based, dielectric fluid pressurized to over 250 psi, fluid leaks create major environmental issues. For the utility provider, mitigating the leaks and repairing their transmission lines were top priorities.
Problem & Prior Solution
The utility company had a repair plan in place that relied on traditional repair methods and worked quickly to try to mitigate the problem.
Traditionally, active leaks were fixed by freezing the pipe with liquid nitrogen on either side of a leak location to alleviate the need for system depressurization and reduce risk of conductor damage. Once the fluid was frozen, a pipe-repair clamp was applied to temporarily stop the leak. An external metal sleeve or barrel was then welded to the host pipe, completely enclosing the temporary repair clamp. Welding external metallic barrels is a typical repair procedure for both leaks and thin spots on pipe-type cables.
Due to the frequency of leaks on these circuits, the service provider created a program to proactively excavate these pipes and perform thorough inspections of the host pipe using both visual inspection and Ultrasonic Thickness (UT) analysis.
Before inspections could be performed, the existing coating had to be completely abated from the pipe surface. This proved to be a costly and hazardous removal process as the coating contained asbestos. After full coating removal, the pipe exterior was inspected and any areas found below a minimum wall thickness were marked for repair. A metal barrel was then welded to the host pipe to completely enclose any corrosion areas, forming a secondary pressure boundary to ensure leaks do not reach the soil. The entire section of pipe was then wrapped with a corrosion-resistant tape before being reburied.
Challenge
A minimum of 20 years of service life had been expected for pipes repaired with traditional methods. However, some sections began to experience new dielectric fluid leaks less than five years after the welded barrel repair technique was used, with especially problematic areas experiencing multiple leaks per month. The company’s engineering team formed a task force to work with vendors to develop an alternative solution to structurally reinforce the external steel pipe on these pipe-type cable systems. The engineering task force sought a solution based on strict system requirements.
The utility provider needed the system to:
- Have a minimum expected service life of 50 years;
- Be able to enclose the existing asbestos containing coating, reducing the amount of hazardous chemical removal required;
- Be able to withstand internal operating pressures up to 1,000 psi even with a through-wall failure on the host pipe;
- Be installed on the streets of a major urban area, in an efficient and cost-effective manner;
- Prevent further corrosion on the host pipes and be compatible with both existing barrel repairs and preexisting cathodic protection system(s);
- Withstand liquid nitrogen exposure for any required repairs without affecting the pressure capacity and performance;
- Meet or exceed all the above standards and be verified through in-person testing by the internal engineering team.

Hydrostatic testing performed to ensure system could withstand internal operating pressure of up to 1000 psiM
Advanced FRP Systems’ Solution and the Pilot Project
Advanced FRP Systems collaborated with the utility task force to develop a solution for the system. After thorough research and development, our corrosion experts developed a composite carbon fiber reinforcement solution that met or exceeded all established system requirements.
The utility provider commissioned a pilot project with Advanced FRP Systems to ensure installation could be performed in the expected field conditions. After a comprehensive contractor training, the installation went forward successfully, even in frigid January weather. The delivered system integrated seamlessly with the existing cathodic protection system and promised to provide the utility with more than 50 years of maintenance-free service.
With this success, a larger, second pilot project was initiated to confirm the cost-effectiveness of Advanced FRP’s solution for large runs of pipe. A two hundred linear-foot section of 5-inch and 10-inch internal diameter (ID) pipe was fully encapsulated and reinforced under close oversight of the utility team and Advanced FRP Systems.
During the installation, a rigorous quality control program was developed to ensure the continued quality of the application and inspection. The application was once again performed on-time without issue or budgetary concerns.
Strategic Solution
After Advanced FRP Systems successfully completed the research, development, testing and field implementation phases for repairing the provider’s HPFF lines with carbon fiber composites, the client looked to other areas within its system that were in need of repair. They found similar corrosion on high-pressure, gas-filled (HPGF) transmission lines at a river crossing. Numerous through-wall failures were present in the gas-filled pipes, which required multiple temporary leak repair solutions to allow composite system installation and curing to full pressure capacity.
The pipe section to be rebuilt was vertical and required engineered pipe supports due to the existing corrosion on the supports to brace the newly-reinforced pipes. Typically, through-wall failures are addressed with a range of solutions including pipe clamps, welded sleeves, and fast-cure polymeric wraps, depending on situational demands.
Advanced FRP Systems undertook a major project to reinforce and prevent leaks of these transmission lines. Our expert team, in conjunction with the approved applicator, addressed all through-wall failures, and repaired and reinforced over 1,200 linear feet of HPGF pipe-type cable using high-strength carbon fiber composite. Even with a maximum pressure rating of greater than 1,000 psi, the composite reinforcement added less than one-fifth the weight of the original host pipe. This alleviated any need for specially-designed pipe supports.
Results to Date
Since 2016, Advanced FRP Systems’ carbon fiber composite solution has been used to refurbish over 12,000 linear feet of pipe-type cable for this utility provider using a structurally-independent, carbon fiber composite pipe built around the existing external steel pipe. Since the initial pilot project, the provider’s confidence in the solution has grown each year, with linear footage repaired annually increasing from less than a hundred linear feet in 2016 to over six thousand linear feet in 2019. Our expert teams performed repairs in especially problematic areas where stray current from other critical infrastructure increased the corrosion rate on the pipe-type cables leaving host pipe regions with very little wall thickness left. These circuits had numerous welded sleeve repairs of varying sizes and lengths covering more than 25 percent of the linear length which made composite wrapping more challenging.
The solution has proven to be extremely reliable in eliminating leaks in previous problem areas and preventing further degradation of the pipe-type cables, despite stray current enhanced corrosion. The composite system is fully compatible with the existing impressed current, cathodic protection system and will provide the utility with a long-term maintenance-free service of these sections of pipe-type cables. Moreover, the provider has made an investment to have their internal maintenance team become certified applicators of our system.
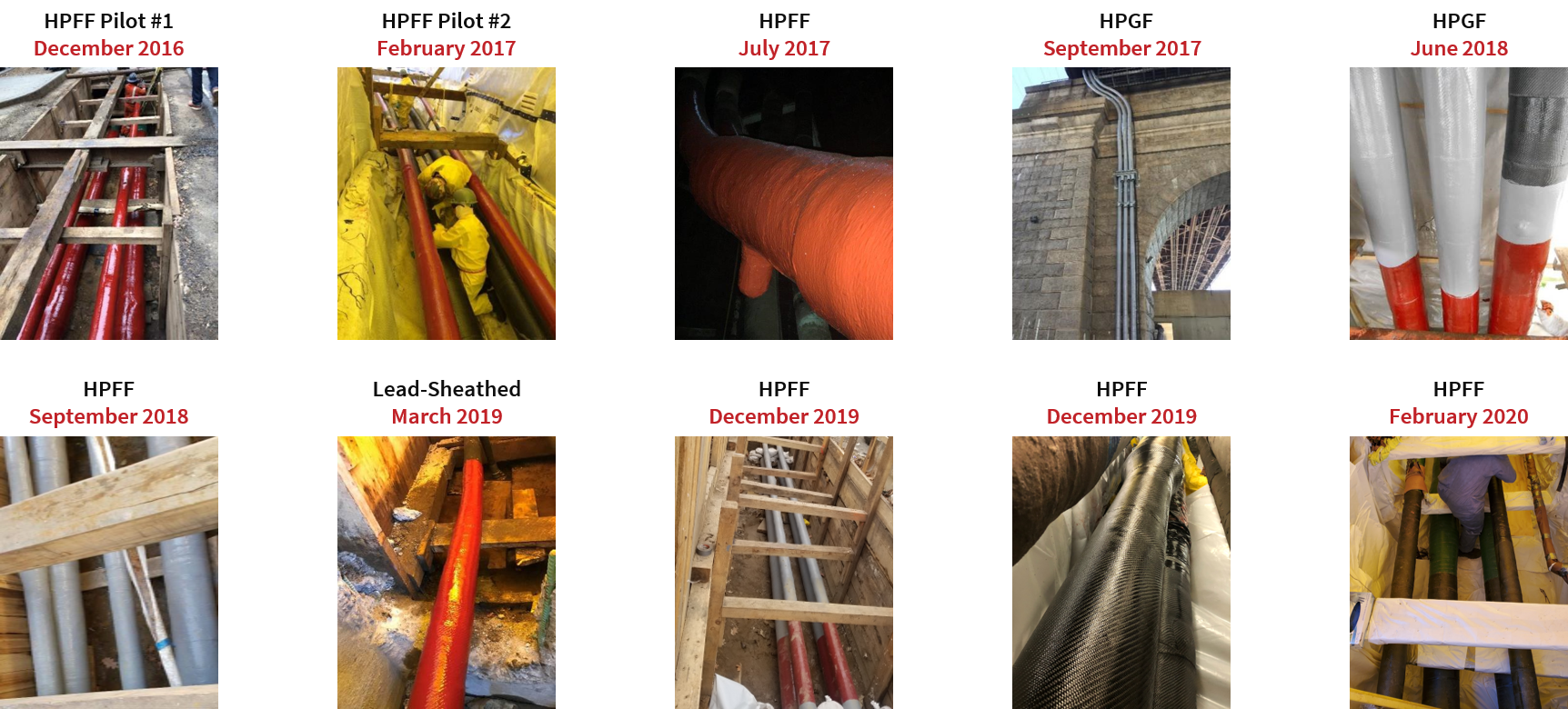
Carbon fiber composite projects completed to date.
Having Issues with Pipe Corrosion or Erosion?
Contact us for a free evaluation!
X